Thermal cracking
- The wall thickness of the casting changes suddenly, which is easy to produce stress concentration when the alloy solidifies; The high sulfur content in molten metal makes the metal material hot brittle; The casting shrinkage is hindered by the gating system; The concession of mold and sand core is poor, the core bone structure is inappropriate, and the sand consumption is too small.
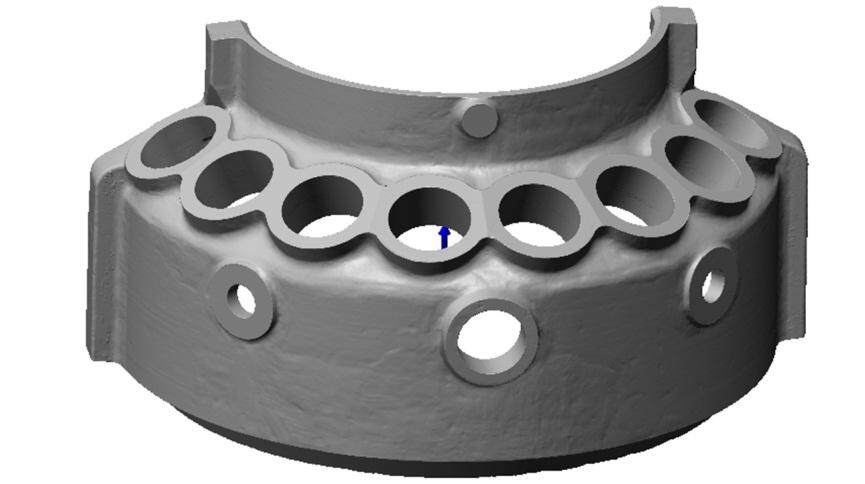
- Prevention methods. The design of castings should try to avoid sudden changes in thickness; The corner of the casting shall be made into appropriate rounded corners, and cold iron or process ribs can be used in the parts of the casting that are prone to tensile stress and the parts that solidify late; The cross-section of a single ingate should not be too large. Try to use multiply scattered ingates. Try to avoid the formation of hot spots at the junction of the innate and the casting and the junction of the gating riser and the casting.
There should be properly rounded corners at the position, and the shape and location of the pouring and riser should not hinder the shrinkage of the casting; The collapsibility of molding sand core can be improved by adding an appropriate amount of sawdust or binder into clay sand; Molding sand and sand core should not be pounded too tightly; Use a suitable core bone with enough sand on the outside.
Cold septum
- The pouring temperature of molten metal is low and the fluidity is poor; The design of the gating system is unreasonable, the number of ingates is small, the cross-sectional area is small, the height of the sprue is too low, and the metal hydraulic head is not enough; Liquid metal is blocked in the cavity.
- Prevention methods. Increase pouring temperature, improve the smelting process, prevent liquid metal oxidation and improve fluidity; Improve the pouring operation to prevent large pieces of slag from blocking the plug opening, and the flow cannot be cut off during the pouring process; Reasonably arrange the pouring system, increase the sectional area of the gate, increase the number of ingates or change their positions, and use a higher upper box or sprue cup to strengthen the inspection of the alignment and fastening of the mold, to prevent the fire from escaping at the parting surface and the air hole of the sand core; Change the pouring position of the casting, and try to put the thin-wall large plane under it or adopt inclined pouring; The wall thickness of castings shall not be too small; Improve the air permeability of molding sand, and properly set the air outlet riser.
Sand inclusion and scarring
- Tight and uneven in modeling; The sand inclusion resistance of molding sand is poor; Improper pouring position.
- Prevention methods. Starting with reducing the expansion force of molding sand, pulverized coal, asphalt, heavy oil, sawdust, etc. are added to the molding sand to cushion the expansion of molding sand; The wet type uses high-quality bentonite to improve the wet strength; The particle size of molding sand should be coarser to improve the permeability of molding sand, and more air holes should be punctured on the sand mold; When modeling, strive for uniform compactness to avoid excessive local compactness of sand mold; Strictly control the moisture of molding sand, and the moisture should not be too high; Nails can be inserted at the molding sand that is prone to defects to prevent the surface from peeling off; Properly reduce the pouring temperature and shorten the pouring time, so that the molten metal can quickly and evenly fill the mold cavity.
Make a purchase of best cast iron, best cast iron skillets, cast iron price from China, you can get them at a good price if you have a large quantity. We hope to be your long-term partner.